DC Motor or Direct Current Motor
What is DC
Motor?
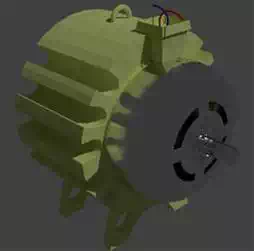
Electrical
motors are everywhere around us. Almost all the electro-mechanical
movements we see around us are caused either by a AC or a DC motor.
Here we will be exploring DC motors. This is a device that converts DC
electrical energy to a mechanical energy.
Principle of DC Motor
This DC or direct current motor works on the principal, when a current carrying
conductor is placed in a magnetic field, it experiences a torque
and has a tendency to move.
This is known as motoring action. If the direction of current in
the wire is reversed, the direction of rotation also reverses. When magnetic
field and electric field interact they produce a mechanical force, and based on
that the working principle of DC motor is established.
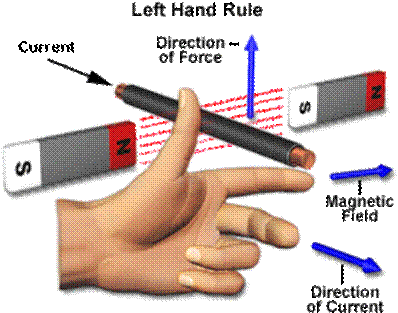
The direction of rotation of a this motor is given by Fleming’s left hand rule,
which states that if the index finger, middle finger and thumb of your left
hand are extended mutually perpendicular to each other and if the index finger
represents the direction of magnetic field, middle finger indicates the
direction of current, then the thumb represents the direction in which force is
experienced by the shaft of the DC motor.
Structurally and construction wise a direct current motor is exactly similar to
a DC generator, but electrically it is just the opposite.
Here we unlike a generator we supply electrical energy to the input port and
derive mechanical energy from the output port. We can represent it by the block
diagram shown below.
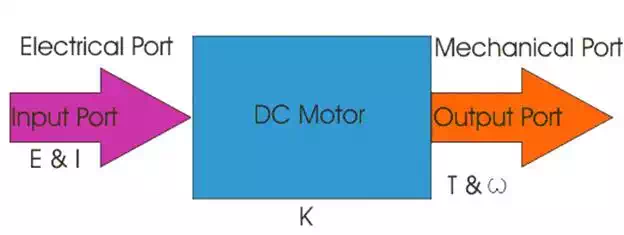
Here in a DC motor, the supply voltage E
and current I is given to the electrical port or the input port and we
derive the mechanical output i.e. torque T and speed ω from
the mechanical port or output port.
The input and output port variables of the direct current motor
are related by the parameter K.

So from the picture above we can well understand that motor is just the opposite
phenomena of a DC generator, and we can derive both motoring and generating
operation from the same machine by simply reversing the ports.
Detailed Description of a DC Motor
To understand the DC motor in details let’s consider the diagram below,
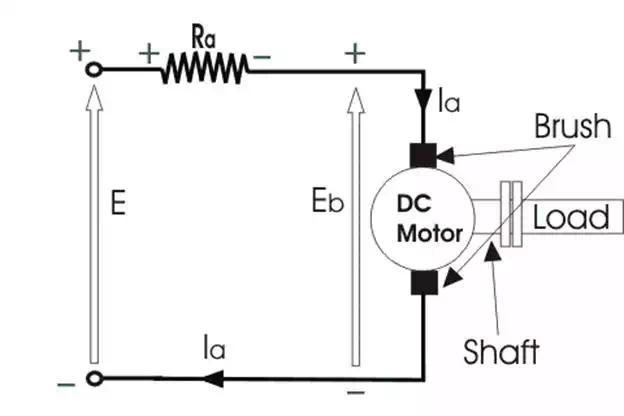
The direct current motor is represented by the circle in the center,
on which is mounted the brushes, where we connect the external terminals, from
where supply voltage is given. On the mechanical terminal we have a shaft
coming out of the Motor, and connected to the armature, and the armature-shaft
is coupled to the mechanical load. On the supply terminals we represent the
armature resistance Ra in series. Now, let the input voltage
E, is applied across the brushes. Electric current which flows through the
rotor armature via brushes, in presence of the magnetic field, produces a
torque Tg.
Due to this torque Tg the
dc motor armature rotates. As the armature conductors are carrying currents and
the armature rotates inside the stator magnetic field, it also produces
an emf Eb in
the manner very similar to that of a generator. The generated Emf Eb is
directed opposite to the supplied voltage and is known as the back Emf, as
it counters the forward voltage.
The back emf like
in case of a generator is represented by

Where, P = no of poles
φ = flux per
pole
Z= No. of conductors
A = No. of parallel paths
and N is the speed of the DC Motor.
So, from the above equation we can see Eb is
proportional to speed ‘N’. That is whenever a direct current motor rotates, it
results in the generation of back Emf. Now lets represent
the rotor speed by ω in rad/sec. So Eb is
proportional to ω.
So, when the speed of the motor is reduced by the application of load, Eb decreases.
Thus the voltage difference between supply voltage and
back emf increases
that means E − Eb increases.
Due to this increased voltage difference, armature current will increase and
therefore torque and hence speed increases. Thus a DC Motor is capable of
maintaining the same speed under variable load.
Now armature current Ia is
represented by

Now at starting,speed ω = 0
so at starting Eb =
0.

Now since the armature winding electrical resistance Ra is
small, this motor has a very high starting current in the absence of back Emf. As
a result we need to use a starter for starting a DC Motor.
Now as the motor continues to rotate, the back Emf starts
being generated and gradually the current decreases as the motor picks up
speed.
Types of DC Motors
Direct motors are named according to the connection o the
field winding with the armature. There are 3 types:
1. Shunt
wound DC motor
2. Series
wound DC motor
3. Compound
wound DC motor