Introduction: Evaporative casting, consumable or eva-foam casting is a sand casting process where the foam pattern evaporates into the sand mold. A process similar to investment casting, this expendable casting process is predicted to be used for 29% of aluminum and 14% of ferrous casting in 2010. There are two main evaporative casting process lost-foam casting and full moldcasting which are widely used because intricate design can be cast with relative ease and with reasonable expense. The main difference between the two is that in the lost-foam casting unbonded sand is used and in the full-mold casting green sand or bonded sand is used.
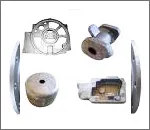
Process: In the first step of evaporative casting, a foam pattern is shaped using material like polystyrene. The pattern is attached with sprues, and gates using adhesives and brushed with refractory substances so that the molds are strong and resistant to high temperature. Refractory covered pattern assembly is then surrounded by a sand mixture to form a mold. In some instances the pattern assembly is mixed in ceramic slurry which forms a shell round the pattern when it dries.
In both cases, the mold in kept at a specific temperature to allow the metal to flow smoothly and enter into every designs and cuts made by the pattern. Molten metal is poured into the mold and the pattern-forming material disappears into the mold. The molten metal takes the shape of the mold and solidifies. When the metal solidifies it is removed from the mold to form the casting.
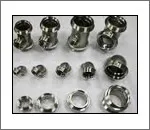
Unlike in the traditional sand casting method, in evaporative sand casting, the pattern does not have to be removed from the mold which reduces the need for draft provisions. Some of the parameter that are used to determine the quality of a eva-foam casting are grain fineness number, time of vibration, degree of vacuum and pouring temperature on surface roughness etc.
Advantages:
· High dimensional accuracy and superior casting surface smoothness · Reduced work process unlike other casting methods · Light weight casting are be done · Casting have improved heat resistance and also abrasion resistance and other cast steel properties · Complicated shapes can be cast without using cores or drafts. |