Shell molding
Shell molding or shell mold casting is a process that can be fully automated, shell molding is the most rapidly used technique for mold and core making. Also known a croning process, this casting technique was invented and patented by J.Croning during World War II. Also know as the process, shell molding technique is used for making thin sections and for acquiring surface finish and dimensional accuracy.
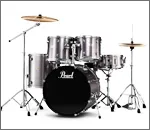
In the first stage of shell molding, a metal pattern is made which is resistant to high temperature and can withstand abrasion due to contact with sand. The sand and resin mixture for the shell mold is brought in contact with the pattern. The mold is placed in an oven where the resin is cured. This process causes the formation of a thin shell around the pattern. The thickness of the mold can be 10-20mm as compared to the heavy mold made for sand castings. When fully cured the skin is removed from the pattern, which is the shell mold.
For each shell molds there are two halves know as the cope and drag section. The two sections are joined by resin to form a complete shell mold. If an interior desing is required, the cores are placed inside the mold before sealing the two parts.
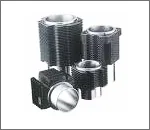
For heavy castings, shell mold are held together by metals or other materials. Now, the molten metal is poured into the mold, and once it solidifies, the shell is broken to remove the casting.This process is highly useful for near net shape castings. Another advantage is that shell molding can be automated.
Automated Shell Molding Machines and Robots: Shell molding machines like the cold shell molding machines helps in making castings with little molding material. In a cold shell molding machine the molds are made using cold binding materials. In it patterns made of wood, metal or plaster can be used. And the greatest benefit is that the mold can be kept horizontally or vertically.
Robotizing: Using robots for shell molding is a milestone for the old molding technology. Robots which are multi functional and re programmable are used in some foundries. Robots are used for a number of activities like robotic gate and sprue removal, robotic cutting of �wedges� for gate valves, robotic core setting, etc. The robots are reliable, consistent, more productive, provides better surface finish, and less machining etc.
Shell Molding Applications: A sizable amount of the casting in the steel industry are made by shell molding process, that ensures better profitability. Carbon steel, alloy steel, stainless steel, low alloys, aluminum alloys, copper, are all cast using shell molding process. Casting that require thin section and excellent dimensional accuracy are cast using this process. Body panes, truck hoods, small size boats, bath tubs, shells of drums, connecting rods, gear housings, lever arms, etc. are cast using croning process.
Advantages of Shell Mold Casting(Shell Molding):
- Thin sections, complex parts and intricate designs can be cast
- Excellent surface finish and goal size tolerances
- Less machining required for the castings
- Near net shape castings, almost 'as cast' quality
- Simplified process that can be handled by semi skilled operators
- Full mechanized and automated casting process
- Less foundry space required.