Rubber Injection Molding
Based off of a process intended for the molding of plastics, injection molding of rubber began in the mid 1960s. Rubber injection molding successfully alters the plastics process by heating the rubber and placing it under significantly more pressure per square inch of cavity surface in molding. This is different from the plastic injection molding process where the materials are cooled under less pressure. Through various innovations, injection molding has become one of the most efficient ways to create molded rubber products in many cases.
The process of injection and injection-transfer molding starts with efficient material preparation. To begin, the material is mixed in bulk and then stripped immediately into continuous approx. 1.25" wide & .375" strips. These strips are then fed into a screw which, in turn, fills a barrel with the appropriate predetermined amount of rubber material.
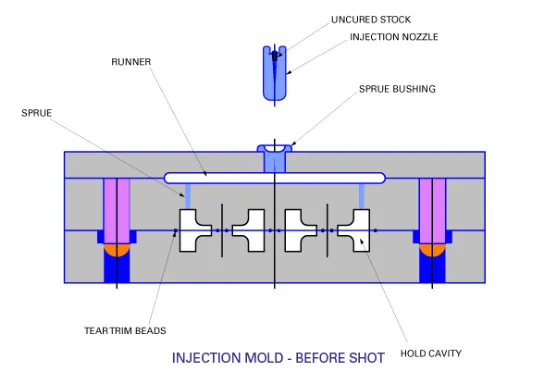
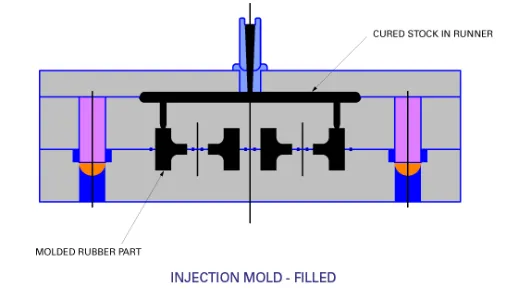
Advantages of injection molding:
- The complete elimination of pre-forms
- The production and need for pre-forms is a labor intensive step that can potentially affect the finished product through variability in pre-form weight and shape.
- Elimination of operator placement of pre-forms.
- Since pre-forms are eliminated, the need for operators to place the pre-forms in a cavity (compression molding) or pot (transfer molding) is removed.
- Injection screw pre-heats material before forcing it into cavities
- This process decreases the viscosity of the material, allowing it to flow more easily into the cavities.
- This pre-heating provides the potential for decreased cure times through
- More rapid cavity filling due to lower viscosity
- Material already being in the curing process through the heat added during screw charging and shear created during injection
- Reduced cycle time
- Flashless tooling
- Economical process for high volumes of medium to high precision components
- Capable of producing overmolded components
- Minimal material waste