Trends In Common Rail Fuel
Injection System
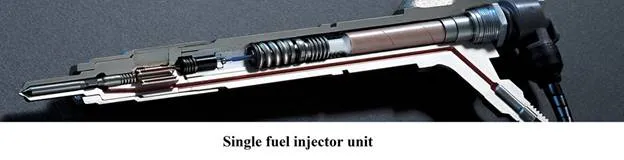
Components of a common rail system
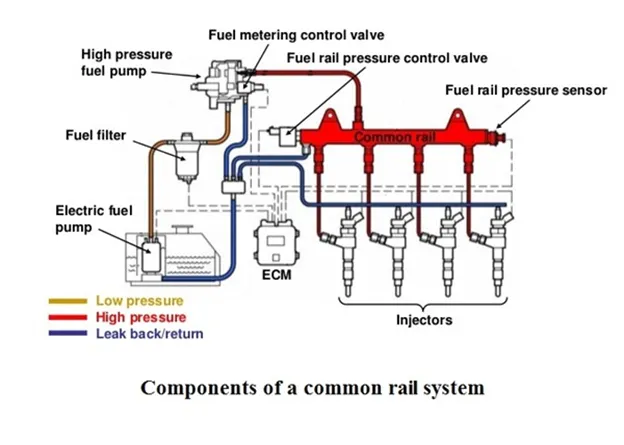
In the common rail system, a pressure sensor measures the fuel
pressure in the rail, its signal valve is compared with the desired value
stored in the engine computer. If the measured value and the desired value are
different, an overflow orifice in the pressure regulator on the high pressure
side is opened or closed. The overflow returns to the fuel tank.
The fuel injectors are opened and closed by the engine computer
at defined times. The duration of injection, the fuel pressure in the rail, and
the flow area of the injector determine the injected fuel quantity. The
injector solenoid valves are controlled according to the accelerator position
and the engine information.
The electronic management in the newer fuel injection systems is
time based control systems-injection timing can therefore be very flexible and
highly precise.
The current advanced fuel injection system such as common rails
can account for 30 to 40 percent of the total engine cost.
Third generation common rail technology is currently available
on the Mercedes E 280 CDI vehicles sold in our country.
Trends in common rail injection system
In the first and second generation of bosch’s common rail the
injection process is controlled by a magnetic solenoid on the injectors. With
an electronic solenoid on the injector nozzle, and electronic controls, pilot
injection becomes possible.
In pilot injection technique, a small quantity fuel is injected
before the main injection. A typical injection period is 300milliseconds. Too
small or too early pilot injection raises the noise, too large increases the
particulate emission. In short the quantity decreases with increasing engine speed and its
interval.
The third generation common rail injection units utilize
piezo-electric injector, which use piezo crystals for even more precise
metering and accurately timed delivery. Piezo crystals deform when a current is
applied across them and return to their original form as soon as the current
supply is switched off. The injector actuators consists of several hundred thin
piezo crystal wafers. In a piezo inline injectors, the actuator is built into
the injector body very close to the jet needle. The movement of the piezo
packet is transferred friction-free, without using mechanical parts, to the
rapidly switching jet needles.
The piezo injectors effect a more precise metering of the amount
of fuel injected and an improved atomization of the fuel in the cylinder.
The third generation common rail fuel injection technology
enabled fuel injectors to run with pressure as high as 2000 bar, while
microsecond fuel delivery timing is possible.
The rapid speed upon which the injectors can switch makes it
possible to reduce the intervals between injections and split the quantity of
fuel delivered into a large number of separate injections for each combustion
stroke.
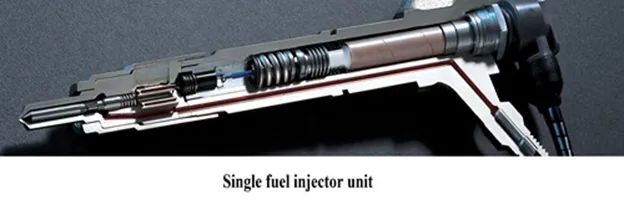
System changes
In modern common rail system, injection is
split into several individual injection such as preinjection, main injection
and post injection. This change will also help in reducing the emissions.
Diesel engine with common rail split injection system has become even
quieter, more fuel efficient, cleaner and more powerful.