CNC Machining Centre
A Machining center is a simply a CNC milling machine with an automatic tool changer and an enclosure.
There are a number of different types of machining centers differentiated by the number of programmable axes.
- Three Axis Machining Center
- Horizontal Three Axis Machining Center
- Four Axis Machining Center
- Five Axis Machining Center
- Machining Center with pallet changer
- Three Axis Machining Center: – A three axis machining center has programmable X and Y axes in the plane of the table and a Z axis in the spindle’s direction. This is the most basic type of machining center, and they start at about $30,000. Typically, three axis machines are in the vertical configuration shown here. Tool changer, control, and enclosure not shown. With three axes, we can machine one surface of a cube with the end of the cutter and four additional surfaces with the side of the cuter.
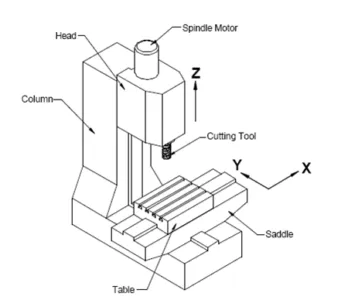
- Horizontal Three Axis Machine:- The illustration depicts a three axis horizontal machining center. Note the different orientation of the X, Y, and Z axes. This type of machine starts at about $90,000. Again, the tool changer, control, and enclosure are not shown. We can still only machine one surface of a cube with
the end of the cutter and four additional surfaces with the side of the cutter.
- Four Axis Machining Center: – Four axis machining centers are generally horizontal, and the table rotates to create the forth axis. True four axis machines start around $100,000 We can also do this by adding a CNC controlled rotary table to a three axis vertical machine, and this is commonly done for small parts. Frequently, a fixture called a tombstone (see sketch later) is mounted on the table and many small parts machined at once on a large machine. We can machine four surfaces of a
cube with the end of the cutter and two additional surfaces with the side of the cutter.
- Five Axis Machining Center: – Be prepared to spend about $250,000 for a true five axis machine. Notice that it is very similar to the four axis machine except the spindle rotates from horizontal to vertical. These machines are used to machine complex parts and molds in the aerospace and automotive industries. We can machine five sides of a cube with the end of the cutter and six sides with the side of the cutter. Besides complex geometry, we can often machine a part in one setup
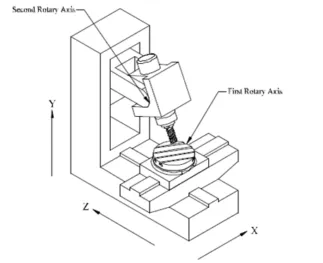
on a five axis machine that would require two or more setups in a simpler machine. This results in a more accurate part.
- Machining Center with Pallet Changer: – Most machining centers can be fitted with a pallet changer to increase productivity. On a plain machine, it sits idle while the operator removes the completed parts and loads the fixture with new ones. With a pallet changer, the operator unloads and reloads one pallet while the machine works on the other. This way, the machine continuously cuts parts.
Machining Centre
Machining centers are very important type of CNC machine tools and are multi-function machines equipped with automatic tool changes and are capable of carrying out milling, drilling, reaming, tapping, boring, counter boring and allied operations without operator intervention for change of tools. Tool changing is carried out using an automatic tool changer and is accomplished in 4-6 seconds.
Step-wise Approaches to CNC Machine Center Development
- Development of CNC machine centers begins with vertical spindle configuration includes 3-axis. Two axes for table and third axis for the spindle head.
- Further turret machining center is developed auto tool selection by indexing the required tool without operator during the CNC programmed and manual tool change is completely removed.
- It has developed by the introduction of a tool library or Tool magazine, where which we can store large number of tools in tool magazine with an auto tool changer for automatically retrieve tool from the tool magazine to the spindle and vice versa.
- Pertaining to a prism type job in a single setup, the concept of the horizontal machining centre developed and increased with an index or rotary table to orient the work piece for machining on various faces.
- Introduction of auto pallet changes, the idle time of machine like setting the job. Setting the tool, setting table has been fully eliminated.
- Auto pallet changer is that, after the complete of machining operation of a job without loss of time and without user, auto pallet change having raw work piece could be exchanged automatically.
Features of Machining Centers
- Higher spindle speed 10,000-30,000 rpm.
- Higher rapid traverse 40 to 60 meters / minute.
- Quick and faster tool changing system.
- It has digital servo control system of main spindle for accuracy.
- It has very efficient thermal control system on various machine elements like main spindle, balls and ball screws and ball bearings for accuracy