Center Pivot Irrigation
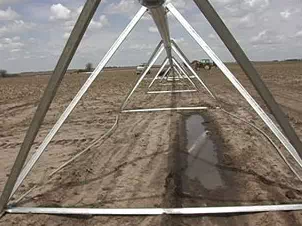
Early center pivot irrigation systems showed a
lot of potential, but they also broke down. The
broke down too often, even according to Robert Daugherty (right) the principal
owner of Valley Irrigation. "A farmer, when [he]
bought one of [our early systems] bought a headache," Daugherty admits
now. "And some didn't want the headache. But after we got it so it was a
reliable functioning system, why then the sales part of it became infinitely
easier."
Center pivot systems were complex engineering systems that relied
on both old and new technologies. They relied heavily on technologies developed
for other uses for key components --
- Turbine
pumps. In the 1940s, irrigators adapted oil
pumps to raise underground water to the surface. Combined with more
powerful internal combustion and electric motors, these pumps could
deliver water under pressure to the new pivot systems.
- Pipes. After
World War II, more and more irrigators started using steel or aluminum
pipes – either with sprinklers or with gates to flood plant rows – to
water their fields. Pivots raised the same pipes off the ground and moved
the pipes around automatically.
- Sprinklers. In
the early 1900s, urban areas had pressurized water systems and used new sprinkler
heads to water lawns in town. Gradually, plant nurseries adapted the
sprinklers to their use and then farmers combined sprinklers with high
pressure pumps and pipes. In 1946, sprinklers irrigated less then 250,000
acres of farmland. By 1959, 3.4 million acres were under sprinklers.
Frank Zybach took new pumps, pipes and sprinklers, put them
together and raised the system off the ground. He supported the system with a
series of towers and figured out how to rotate the entire apparatus around a
central pivot point. Zybach, Daugherty and all the engineers and inventors who
followed their footsteps had to devise and refine solutions to a whole series
of problems.
- How
to move the pivot around. Zybach's first system siphoned some of the
pressurized water off from the main pipe and sent it into a piston that
pushed a linkage that moved the steel wheels forward. Other inventors used
oil hydraulic pistons to provide power, and still others installed
electric motors on their towers. Rubber wheels replaced steel fairly
quickly. Now, the majority of systems use electric motors to drive rubber
wheels. They can go both backwards and forwards at controlled speeds.
- Keeping
the towers in line. All center pivot systems will set the overall speed of
the system by governing the tower on the outside of a center pivot circle
– that's the tower that has to travel farther and faster than the towers
toward the center. Then, each manufacturer has developed ways for the
inner towers to sense when they are behind or ahead of the tower farther
out. When one tower gets behind, its motor turns on or runs faster to
catch up. Over the years these control sensors have evolved from simple
mechanical linkages to electronic sensors under computer control.
- Distributing
water evenly. Again, because the pipe travels faster the farther out it
gets, more water has to be distributed at the ends of a pivot system than
in the middle. The manufacturers have adapted more and more sophisticated
sprinkler heads and placed them in precise patterns along the length of
the pipe to provide even coverage. Some of today's systems even use GPS
and wireless communication technology to control how much water gets to
specific portions of the field and to control the system from a cell phone
or remote laptop computer.
- Supporting
the pipe. Water is heavy – 62.5 pounds per cubic foot. The largest pivots
use 10-inch diameter pipe and extend out 2,600 feet. So, the water in that
system can weigh over 88,000 pounds. (Do the math here.) When you raise
those pipes off the ground, you have to support them. Early systems used
wires running from the top of tall towers supporting arched or bowed pipe.
Later, manufacturers developed a truss system that bowed the pipe up and
transferred the weight back to the towers. This "undertruss"
system is most often used today and allows the pipe to be raised higher
than a wire support system does.
- Raising
the pipe high enough. Zybach's first system was only a few feet off the
ground. Corn, one of the most popular crops across America, grows six to
eight feet high (depending on the variety). Raising the pipe high enough
to travel around over the corn made undertruss systems more attractive.
- Getting
electricity down the system. The pivot point of a center pivot system is
stationary. Everything else moves around in a circle. So if you simply ran
a cable up the pivot point and down to the towers, the cable would wrap
around the pivot point and eventually break. So the engineers at the pivot
companies figured out how to bring the power up into a device called a
collector ring. The power from the pivot point is distributed to a series
of stationary circular plates and then connections are made to the wires
that travel down the pivot's pipe spans.
- Keeping
the pipes from rusting. Early pivot systems were built out of steel to
support the weight and pressures of the systems. The steel was painted to
protect it from rust. But paint wears off. So, by the late 1960s, Valley
irrigation systems were being built out of hot-dipped galvanized steel
pipes and components. This protected the steel much better. Later systems
were built from aluminum – which doesn't rust – and even from stainless
steel or plastic coated pipes that can resist highly corrosive water or
chemicals.
Each of these technical innovations borrowed state-of-the-art
engineering and scientific knowledge of the time and was a major step in making
the systems work reliability.