Rocket Science 101: Lightweight rocket shells
This is the fourth and final part of a series of
posts on rocket science. Part I covered the history of rocketry, Part II dealt with the operating principles of rockets and Part
III looked at the components that go into the
propulsive system.


● Using lightweight materials.
● And/or optimising the geometric design of the structure.
The load-bearing structure in a rocket is very
similar to the fuselage of an airplane and is based on the same design
philosophy: semi-monocoque construction.
In contrast to early aircraft that used frames of discrete members braced by
wires to sustain flight loads and flexible membranes as lift surfaces, the
major advantage of semi-monocoque construction
is that the functions of aerodynamic profile and load-carrying structure are
combined. Hence, the visible cylindrical barrel of a rocket serves to contain
the internal fuel as a pressure vessel, sustains the imposed flights loads and
also defines the aerodynamic shape of the rocket. Because the external skin is
a working part of the structure, this type of construction is known as stressed
skin or monocoque. The even distribution of
material in a monocoque means that the
entire structure is at a more uniform and lower stress state with fewer local stress
concentrations that can be hot spots for crack initiation.
Second, curved shell structures, as in a
cylindrical rocket barrel, are one of the most efficient forms of construction
found in nature, e.g. eggs, sea-shells, nut-shells etc.. In
thin-walled curved structures the external loads are reacted internally by a
combination of membrane stresses (uniform stretching or compression through the
thickness) and bending stresses (linear variation of stresses through the
thickness with tension on one side, compression on the other side, zero stress
somewhere in the interior of the thickness known as the neutral axis). As a
rule of thumb, membrane stresses are more efficient than bending stresses, as
all of the material through the thickness is contributing to reacting the
external load (no neutral axis) and the stress state is uniform (no stress
concentrations).
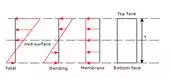
As described above, reducing the wall-thickness
in a monocoque construction greatly helps to reduce the mass of the structure.
However, the bending stiffness scales with the cube of the thickness, whereas
the membrane stiffness only scales linearly. Hence, in a thin-walled structure
we ideally want all deformation to be in a membrane state (uniform squashing or
stretching), and curved shell structures help to guarantee this. However, due
to the large mismatch between membrane stiffness and bending stiffness in a
thin-walled structure, the structure may at some point energetically prefer to
bend and will transition to a bending state.
The advantage of curved monocoques is that their buckling loads are much greater than those flat
plates. For example, you can safely stand on a soda can even though it is made
out of relatively cheap aluminium. However, once the soda can does buckle all
hell breaks loose and the whole thing collapses in one big heap. What is more,
curved structures are very susceptible to initial imperfections which
drastically reduce the load at which buckling occurs. Flick the side of a soda
can to initiate a little dent and stand back on the can to feel the difference.
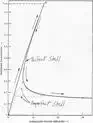
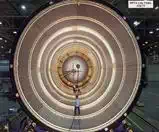
● First, they help to resist compressive loading and therefore remove some
of the onus on the thin skin.
● Second, they break the thin skin into smaller sections which are much
harder to buckle. To convince yourself, find an old out-of-date credit card,
cut it in half and repeat the previously described experiment.
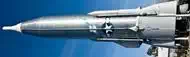
Atlas 2E Ballistic Missile with buckling “diamonds” along the entire
length of the external rocket skin (via Wikimedia Commons)
NASA Langley Research Center has
been, and continues to be, a leader in studying the complex failure behaviour
of rocket shells.